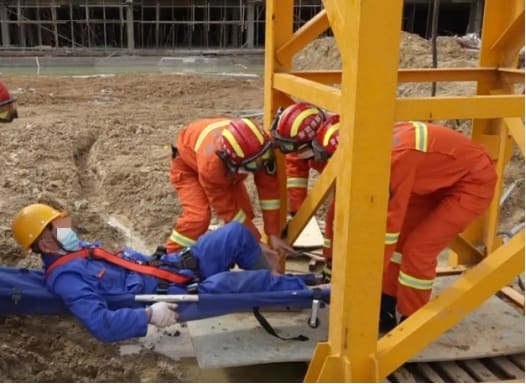
In workplace environments where hazards are present, personal protective equipment (PPE) plays a crucial role in safeguarding employees from serious injuries and health risks. Neglecting to wear safety gear not only puts the individual at risk but can also affect team morale, productivity, and a company’s legal standing. From common injuries to regulatory implications, understanding the importance of PPE is essential for maintaining a safe and efficient work environment.
Failing to wear safety gear can lead to life-threatening injuries, long-term health consequences, decreased productivity, and costly legal repercussions for both employees and employers.
What Are the Most Common Injuries That Occur When Safety Gear Is Not Worn?
Without proper safety gear, workers are more vulnerable to a range of common workplace injuries that vary depending on the industry and work environment.
Common Injuries by Workplace Hazard:
- Head Injuries: Without helmets or hard hats, workers are at high risk of head trauma from falling objects or impacts, common in construction, warehousing, and mining.
- Eye Injuries: Not wearing safety goggles in environments with flying particles, chemicals, or sparks can lead to eye injuries, potentially causing blindness.
- Respiratory Issues: Respirators protect workers from inhaling toxic substances, dust, and fumes. Without respiratory protection, workers are susceptible to respiratory illnesses and poisoning.
- Hand Injuries: Without gloves, workers handling sharp objects, hot surfaces, or chemicals risk cuts, burns, and chemical exposure.
- Hearing Loss: Prolonged exposure to loud noises without ear protection can lead to permanent hearing loss, a common issue in industries like manufacturing and aviation.
Injury Type | Common Cause | Typical PPE Required |
---|---|---|
Head Trauma | Falling objects, impacts | Hard hats, helmets |
Eye Injuries | Debris, chemicals, sparks | Safety goggles, face shields |
Respiratory Issues | Toxic fumes, dust, chemicals | Respirators, masks |
Hand Injuries | Sharp objects, chemicals, heat | Protective gloves |
Hearing Loss | Loud machinery, construction noise | Earplugs, earmuffs |
How Does the Absence of Specific Types of Safety Gear Increase the Risk of Injury in Different Work Environments?
In various industries, specific types of safety gear are essential for protecting workers against particular hazards. The absence of this gear dramatically increases the risk of injury or health issues.
Increased Risks by Industry and Safety Gear:
- Construction: Without hard hats, workers are at risk from falling objects and debris, while a lack of harnesses for heights increases the danger of falls.
- Healthcare: Without gloves, masks, and gowns, healthcare workers risk exposure to infectious diseases and hazardous chemicals.
- Manufacturing: In heavy manufacturing environments, the absence of steel-toed boots, gloves, and goggles exposes workers to crush injuries, cuts, and eye damage.
- Chemical Processing: Without chemical-resistant clothing and respirators, workers face heightened risks of chemical burns and respiratory issues from toxic fumes.
In each of these environments, specific PPE items address unique hazards. Not using these safety items leaves workers vulnerable to injuries that could otherwise be prevented.
What Are the Long-Term Health Impacts of Not Wearing Safety Gear Consistently?
Neglecting to wear PPE consistently can lead to chronic health issues that may affect workers for years, even after they have left their current positions.
Common Long-Term Health Consequences:
- Respiratory Illnesses: Prolonged exposure to dust, chemicals, and fumes without respiratory protection can lead to chronic respiratory diseases like asthma, bronchitis, and even lung cancer.
- Hearing Damage: Workers who are exposed to high noise levels without hearing protection often suffer from irreversible hearing loss or tinnitus, which can affect their quality of life.
- Skin and Eye Damage: Repeated exposure to chemicals without gloves or eye protection can lead to skin conditions, chemical burns, and vision problems.
- Musculoskeletal Issues: Lifting without back support or ergonomic PPE can result in long-term back problems, particularly in industries requiring heavy physical labor.
Over time, these health issues not only diminish a worker’s ability to perform their job but also increase healthcare costs, lead to early retirement, and reduce life expectancy.
How Does Not Wearing Safety Gear Affect Workplace Morale and Productivity?
When employees ignore safety protocols, it can lead to a decline in workplace morale and productivity. Workers who witness others disregarding PPE guidelines may feel that safety isn’t a priority, reducing their confidence in the workplace’s commitment to their well-being.
Key Impacts on Morale and Productivity:
- Increased Stress: Employees may feel anxious if they perceive that safety risks aren’t adequately addressed, which can reduce focus and efficiency.
- Loss of Trust: When management fails to enforce PPE use, workers may lose trust in the company’s dedication to their health, leading to disengagement.
- Reduced Productivity: Injuries resulting from lack of PPE can lead to increased absenteeism, reduced workforce availability, and slower project completion times.
- Higher Turnover: A perceived lack of safety can result in higher turnover rates, as employees seek safer work environments.
When a culture of PPE compliance is established, it fosters a sense of security and respect, which can boost morale and lead to higher productivity.
How Do Regulations and Potential Lawsuits Affect Companies That Fail to Enforce PPE Use?
Employers are legally required to ensure a safe working environment, which includes enforcing PPE use where necessary. Failing to comply with safety regulations can lead to significant legal consequences.
Regulatory and Legal Consequences:
- Fines and Penalties: Organizations like OSHA in the U.S. impose fines on companies that fail to enforce PPE standards, especially in high-risk industries.
- Lawsuits and Compensation Claims: If a worker is injured due to the lack of PPE enforcement, the company may face costly lawsuits or worker’s compensation claims.
- Reputational Damage: Consistently neglecting safety protocols can damage a company’s reputation, making it harder to attract top talent and retain clients.
- Increased Insurance Premiums: Companies with frequent injuries due to non-compliance with PPE regulations may see higher insurance costs.
By enforcing PPE usage and adhering to safety regulations, companies not only protect their employees but also avoid financial and reputational damage.
How Important Is Proper PPE Training in Reducing Workplace Risks and Ensuring Compliance?
PPE is only effective when it’s used correctly, which requires comprehensive training for all employees. Without proper training, workers may not understand the risks of not wearing PPE or how to use it properly.
Components of Effective PPE Training:
- Hazard Awareness: Employees should understand the specific risks in their work environment and why each type of PPE is necessary.
- Correct Use and Fit: Proper training includes how to wear, adjust, and check the fit of PPE to ensure it offers the intended level of protection.
- Maintenance and Replacement: Workers should know how to maintain PPE, identify wear and tear, and replace damaged gear.
- Compliance and Accountability: Training should emphasize the importance of PPE compliance and outline disciplinary actions for not following safety protocols.
With well-designed PPE training programs, companies can reduce workplace risks, enhance compliance, and ensure that all employees are equipped to protect themselves effectively.
Conclusion
Not wearing safety gear at work exposes employees to serious risks, including injuries, long-term health issues, and even fatal accidents. The absence of PPE not only endangers individuals but also affects team morale, productivity, and an organization’s financial and legal standing. By enforcing PPE standards, conducting regular training, and emphasizing safety culture, companies can create a safer workplace that protects employees and maintains high operational standards. PPE is more than just a regulatory requirement—it’s a crucial part of safeguarding health and building a resilient workforce.
Zion Zhang
Recent Posts
5 Essential Personal Protective Equipment (PPE) Items and Their Uses
2025年6月17日When buyers ask me, “Zion, if I can only start with five […]Comprehensive Personal Protective Equipment (PPE) List for Workplace Safety
2025年6月17日As a PPE supplier, I’ve talked to dozens of procurement […]Face Shield Policy: Guidelines for Safe and Effective Use in the Workplace
2025年6月17日A buyer once told me, “Zion, we’ve got face shields in the […]Understanding the Importance of Limb and Body Protection in Hazardous Environments
2025年6月16日Not long ago, a buyer from a food processing plant reached […]Essential PPE for Staying Safe During Protests and Demonstrations
2025年6月13日I once spoke with a buyer who handled safety gear for NGOs […]WorkSafeBC Steel Toe Boot Requirements: Compliance, Safety Features, and Industry Applications
2025年6月13日I still remember the first time a Canadian client called me […]
CONTACT US
- Feel free to contact us any time. We will get back to you as soon as we can!
- +86-17330061805